Understanding the Role of an **Injection Moulding Manufacturer** in Modern Industry
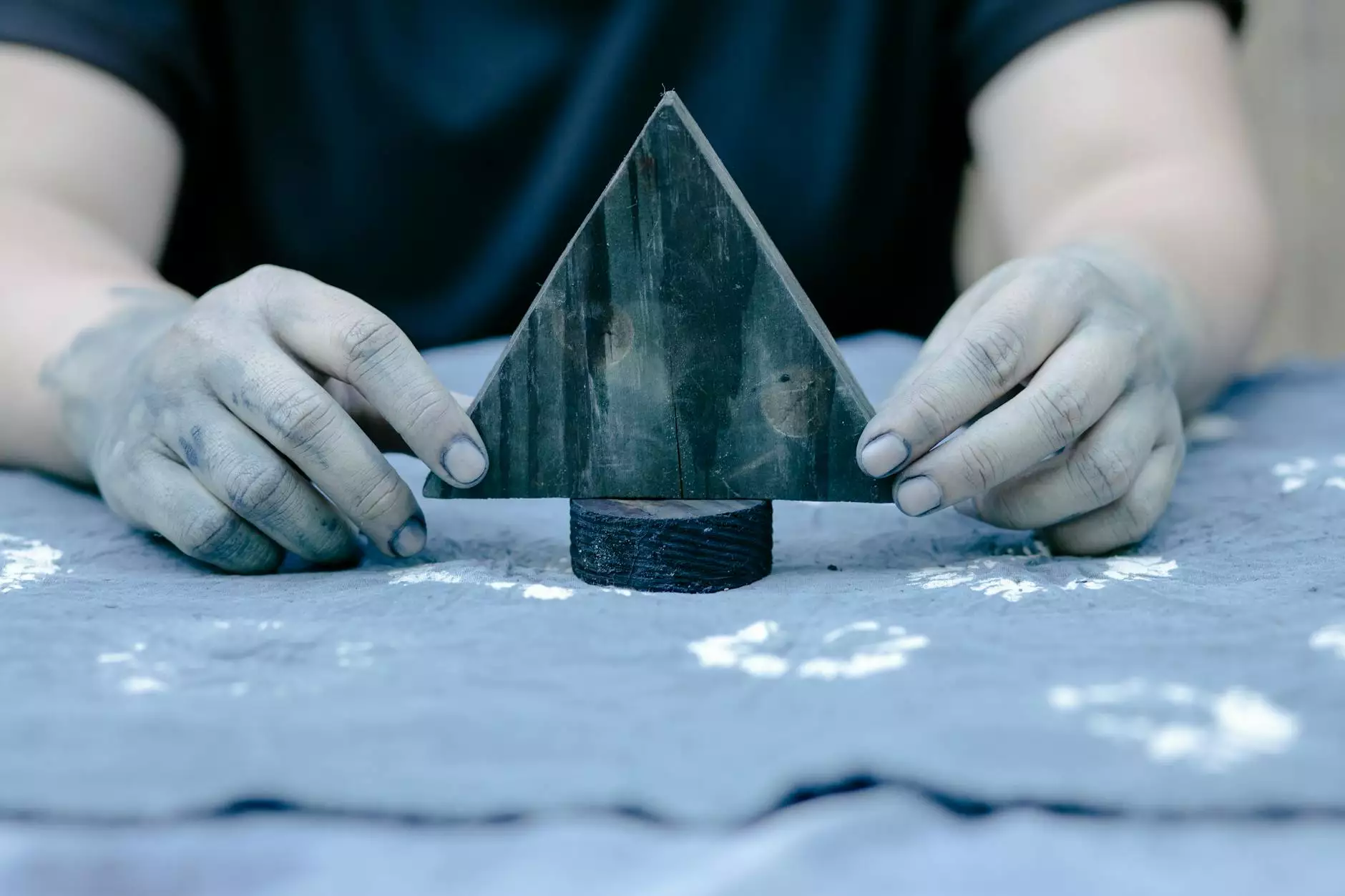
The rise of precise manufacturing techniques has transformed various industries, and among these, the role of an injection moulding manufacturer has become increasingly critical. Injection moulding stands as one of the most efficient methods for producing high-quality plastic parts, which are integral in numerous applications, from automotive to consumer goods. This article delves into the intricacies of this manufacturing process, the significance of quality, and the competitive edge provided by premier manufacturers like DeepMould.net.
What is Injection Moulding?
Injection moulding is a manufacturing process used to produce parts by injecting molten material into a mould. This method is utilized for manufacturing a vast array of products, mainly plastics, and has expanded to include metal, glass, and other materials. The benefits of injection moulding include:
- High Efficiency: The process allows for mass production of identical items at rapid speeds.
- Complex Designs: Injection moulding can create intricate shapes that would be difficult or impossible to achieve using other methods.
- Material Versatility: A variety of materials can be used, tailoring products to specific requirements.
- Precision and Consistency: Each piece produced is highly consistent in quality and dimensions.
Applications of Injection Moulding in the Metal Fabrication Industry
Within the realm of metal fabrication, injection moulding serves a crucial function. Manufacturers often need precise and durable components for machinery, equipment, and various tools. The applications include:
- Automotive Parts: Injection moulding is extensively used to create components like dashboards, bumpers, and various fittings.
- Medical Devices: This process is essential for manufacturing components that must meet strict safety and quality regulations.
- Consumer Products: Household items, electronic housings, and packaging solutions frequently utilize injection moulded parts.
- Industrial Equipment: Machinery parts, enclosures, and structural components for various industries often rely on the precision of injection moulding.
The Process of Injection Moulding
Understanding the injection moulding process is essential for appreciating the capabilities of an injection moulding manufacturer. The process consists of several phases:
1. Designing the Mould
The first step in the injection moulding process is the design of the mould. Engineers use advanced CAD software to create detailed designs that meet specific product requirements. The design must consider factors like:
- Part geometry
- Material flow
- Cooling time
- Ease of mould release
- Overall production efficiency
- Cost-effectiveness
- Quality specifications
2. Mould Creation
Once the design is finalized, the mould is manufactured using high-precision machining equipment. This stage is critical, as the mould must be able to withstand high pressures and temperatures during the injection process.
3. Injection Phase
The actual injection of the material occurs when the molten material, usually plastic, is injected into the mould cavity at high pressure. This phase necessitates the right temperature and pressure settings to ensure the material fills the mould completely and adheres to all contours.
4. Cooling Phase
After injection, the mould is cooled to solidify the material. The cooling phase's duration depends on the material type, part thickness, and mould design. Optimizing this phase is crucial for production efficiency.
5. Ejection Phase
Once the part has cooled and solidified, the mould opens, and ejector pins push the part out. A precise ejection process prevents damage to the part and ensures that it remains intact and free from defects.
The Benefits of Partnering with a Leading Injection Moulding Manufacturer
Choosing the right injection moulding manufacturer can significantly impact your business's success. Here are some advantages of collaborating with a top-tier provider:
1. Quality Assurance
High-end manufacturers implement rigorous quality control measures throughout the production process. From material sourcing to final inspections, quality assurance ensures that every part meets or exceeds industry standards.
2. Advanced Technology and Expertise
Leading manufacturers like DeepMould.net invest in the latest technology and machinery, allowing them to produce complex parts with incredible precision. Their teams of engineers and technicians have extensive expertise in injection moulding, enabling them to tackle unique challenges effectively.
3. Customization and Flexibility
In today's market, customization is key. A proficient injection moulding manufacturer can adapt designs to meet the specific needs of clients and ensure a tailored manufacturing process, whether for small or large-scale production runs.
4. Cost Efficiency
By optimizing the production workflow and utilizing advanced technology, leading firms can provide competitive pricing without sacrificing quality. This cost efficiency can significantly enhance a company's bottom line.
Sustainability in Injection Moulding Manufacturing
In recent years, sustainability has become a focal point for all manufacturing sectors, including injection moulding. Top manufacturers are adopting eco-friendly practices to reduce waste and promote recycling. Key initiatives include:
- Using biodegradable materials when possible
- Implementing closed-loop systems to reuse excess plastic
- Reducing energy consumption through efficient machinery
- Minimizing packaging waste by optimizing shipment logistics
Challenges Faced by Injection Moulding Manufacturers
Despite its numerous advantages, the injection moulding industry does face challenges, including:
1. Material Costs and Sourcing
The prices of raw materials can fluctuate significantly, affecting overall production costs. Reliable sourcing and supplier relationships are essential for mitigating this risk.
2. Technological Changes
With rapid technological advancements, manufacturers must continually invest in new technologies to stay competitive, which can be financially challenging.
3. Meeting Tight Deadlines
Increased demand for quicker turnaround times can pressure manufacturers, making efficient production scheduling and workflow management vital components of success.
Conclusion: The Future of Injection Moulding Manufacturing
The future of the injection moulding manufacturer sector looks promising, driven by innovation and an increasing demand for customized solutions. As companies like DeepMould.net lead the charge by adopting cutting-edge technologies and sustainable practices, they pave the way for a more efficient and eco-friendly manufacturing landscape.
Investing in an injection moulding partner who prioritizes quality and innovation is crucial for businesses wanting to stay ahead in competitive markets. By leveraging the unique capabilities of professional manufacturers, companies can realize their visions and achieve remarkable growth.
Contact DeepMould.net for Your Injection Moulding Needs
If you are in search of a reliable and high-quality injection moulding manufacturer, look no further than DeepMould.net. Our commitment to excellence, sustainable practices, and client satisfaction makes us the ideal partner for your manufacturing needs. Visit us today to learn more about how we can help bring your ideas to life!