Understanding GRP Manufacturers: A Comprehensive Guide
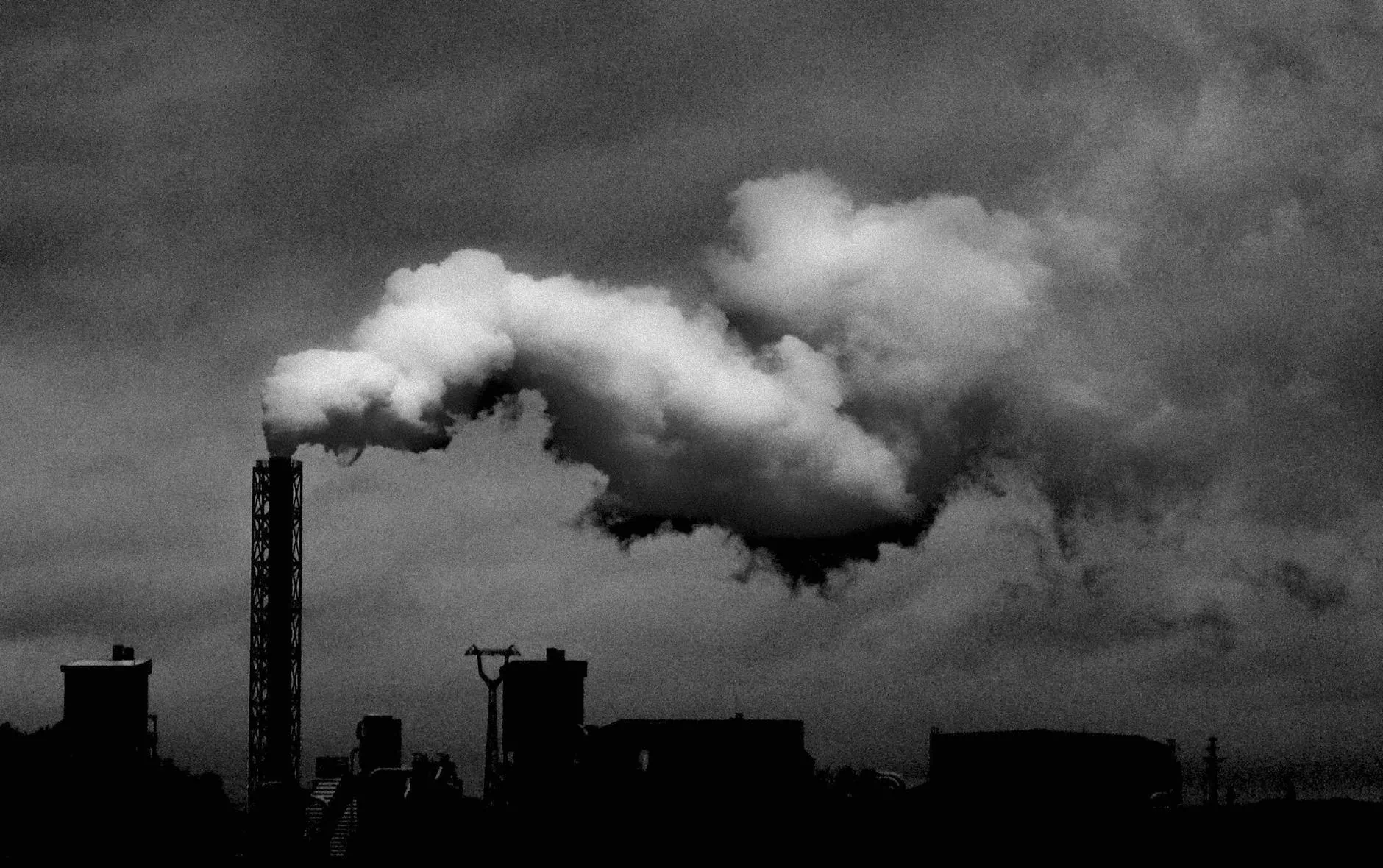
Glass Reinforced Plastic (GRP), also known as fiberglass, is a composite material that has gained immense popularity across various industries due to its lightweight and durable nature. In this article, we will dive into the intricacies of GRP manufacturers, exploring their processes, benefits, applications, and much more.
The Role of GRP Manufacturers
GRP manufacturers are pivotal in producing high-quality fiberglass products. These manufacturers utilize advanced technology and expertise to create materials that meet the stringent demands of different sectors including construction, automotive, marine, and more. The role they play is essential for ensuring that products are not only effective but also durable and sustainable.
What is GRP?
Glass Reinforced Plastic (GRP) is a composite material made by combining a polymer matrix with glass fibers. This material has remarkable strength-to-weight ratios, corrosion resistance, and versatility, making it suitable for a wide array of applications.
Benefits of GRP
- Lightweight: GRP is significantly lighter than conventional materials like metal, which leads to lower transportation costs.
- Strength and Durability: It exhibits high tensile strength and impact resistance, making it ideal for demanding situations.
- Corrosion Resistance: GRP is naturally resistant to various chemicals and corrosive environments.
- Versatility: It can be molded into complex shapes, offering flexibility in design.
- Low Maintenance: Products made from GRP require minimal maintenance over their lifespan.
Overview of the GRP Manufacturing Process
The manufacturing process of GRP involves several key steps, each critical to producing a high-quality final product. Here’s a detailed overview:
1. Material Selection
It all starts with selecting the right raw materials. The most commonly used fibers are glass fibers, while the matrix is typically a polyester or vinyl ester resin. The choice of materials impacts the quality and properties of the final product.
2. Fabrication Methods
There are several fabrication methods employed by GRP manufacturers, including:
- Hand Lay-Up: This manual process involves laying fiberglass sheets into a mold, applying resin, and then allowing it to cure.
- Spray-Up: A combination of chopped fibers and resin is sprayed into a mold, which is ideal for larger components.
- Filament Winding: Continuous strands of glass fibers are wound over a rotating mandrel, suitable for cylindrical shapes like pipes.
- Prepreg Lay-Up: Glass fibers pre-impregnated with resin are laid in a mold and cured under heat and pressure.
3. Curing Process
After fabrication, the GRP components undergo a curing process where the resin hardens, providing strength to the structure. This can involve atmospheric curing or using an oven for heat curing.
4. Trimming and Finishing
Final products are often trimmed and finished to meet quality standards and customer specifications, ensuring that they are ready for use.
Applications of GRP
The versatility of GRP makes it applicable in numerous industries. Here are some of the most common uses:
1. Construction Industry
In construction, GRP is used for:
- Roofing: Lightweight and durable roofing solutions.
- Cladding: Aesthetic and functional facade panels.
- Bathroom Pods: Factory-manufactured units that streamline construction.
2. Automotive Sector
In the automotive industry, GRP is utilized for:
- Body Panels: Lightweight panels that improve fuel efficiency.
- Interior Components: Dashboard elements and trim that reduce overall vehicle weight.
3. Marine Applications
The marine sector benefits from GRP’s corrosion resistance with applications such as:
- Boat Hulls: Durable hulls that withstand harsh marine environments.
- Decks and Fittings: Lightweight and strong solutions for various marine fittings.
4. Electrical Industry
GRP is used in the electrical industry for:
- Electrical Enclosures: Protective housings for sensitive electrical equipment.
- Pole and Tower Construction: Components that require high strength and light weight.
Environmental Impact of GRP Manufacturing
As industries worldwide seek more sustainable practices, GRP manufacturers are also adapting. Here’s how they are making a difference:
1. Use of Recyclable Materials
Many GRP manufacturers are beginning to use recyclable materials in their production processes, thereby reducing waste and promoting sustainability.
2. Energy Efficiency
Manufacturers are also implementing energy-efficient processes and machinery to minimize their carbon footprint.
3. Waste Management
Proper waste management strategies are critical in the GRP production process, reducing environmental impact through recycling and responsible disposal of unused materials.
Choosing the Right GRP Manufacturer
When selecting a GRP manufacturer, consider the following factors:
- Experience: Look for manufacturers with a proven track record in the industry.
- Quality Assurance: Ensure they follow strict quality control processes to guarantee product standards.
- Customization Capabilities: The ability to tailor products to specific needs is essential.
- Technology: Advanced manufacturing techniques and technologies should be a priority.
- Customer Support: A reliable support system can make a significant difference in your overall experience.
Future Trends in GRP Manufacturing
The future of GRP manufacturing is bright, driven by innovation and technology advancements. Here are some trends to watch:
1. Advanced Materials
Research into advanced materials, including bio-based resins and carbon-fiber composites, is on the rise, promising even more sustainable solutions.
2. Automation and Robotics
Increasing automation in manufacturing processes will lead to greater efficiency, precision, and reduced labor costs.
3. 3D Printing Techniques
3D printing is making inroads into GRP production, allowing for rapid prototyping and custom parts manufacturing.
4. Focus on Circular Economy
The shift towards a circular economy is prompting manufacturers to rethink production cycles and waste management.
Conclusion
In conclusion, the role of GRP manufacturers in today’s industry is vital, offering solutions that are not only efficient and innovative but also environmentally conscious. From contributing to sustainable practices to providing high-quality materials for diverse applications, these manufacturers push the boundaries of what is possible with composite materials.
As industries continue to evolve, so will the technologies and practices of GRP manufacturing, paving the way for a future that embraces both quality and sustainability.