The Essential Guide to Silicone Sheets for Vacuum Presses
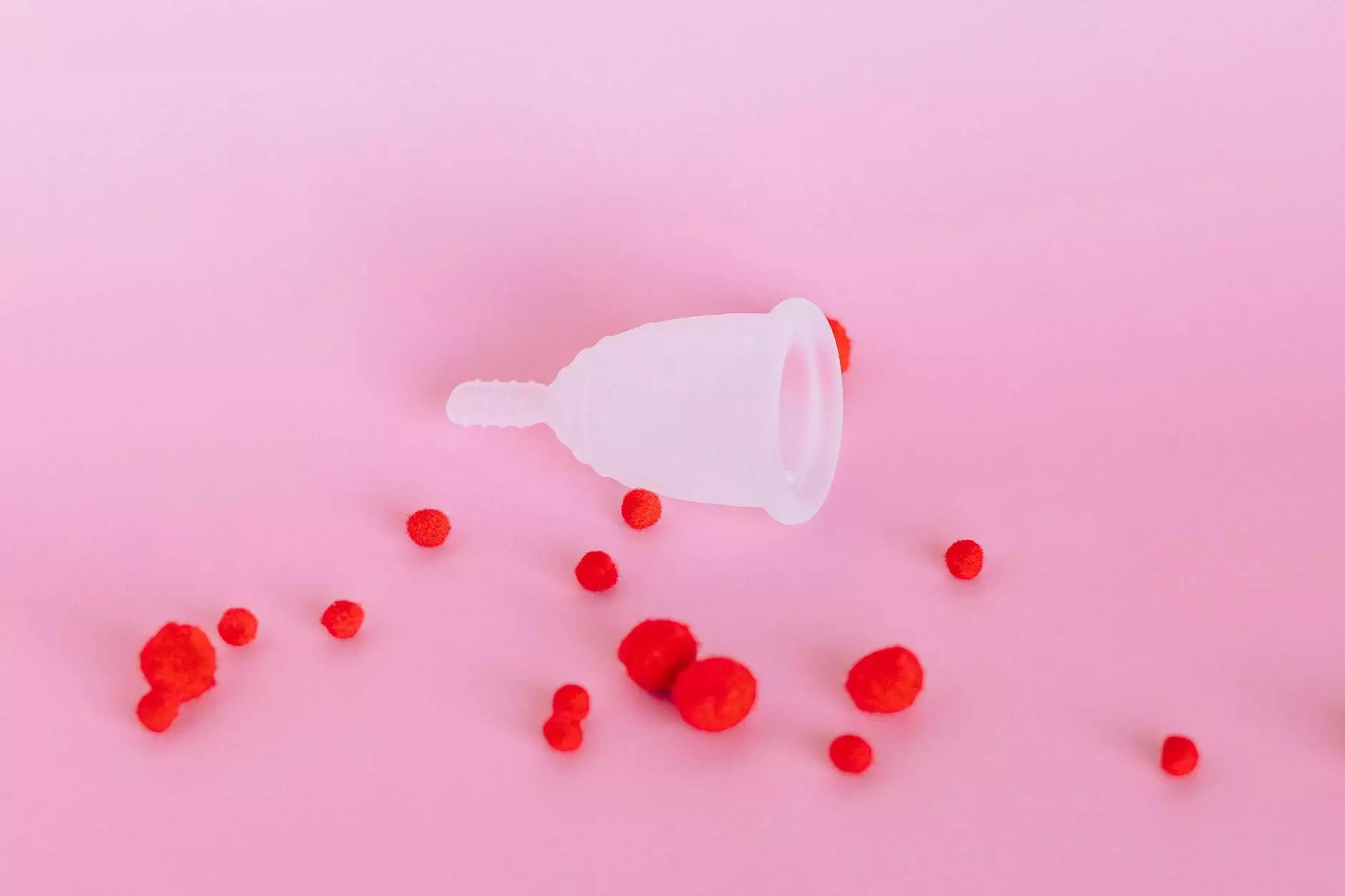
Silicone sheets for vacuum presses are indispensable tools in the realm of manufacturing, woodworking, and many other industries. Understanding their functionality, advantages, and application can significantly elevate your business capabilities. In this comprehensive guide, we will delve deep into the world of silicone sheets, demonstrating how they can optimize your operational processes while ensuring the best results.
What Are Silicone Sheets?
Silicone sheets are flexible, durable, and heat-resistant materials made from silicone polymer. Their unique properties make them ideal for use in vacuum presses, where precision and reliability are paramount. These sheets serve as a barrier between your products and the vacuum press, ensuring that materials like wood, composites, and plastics adhere correctly while undergoing processes such as laminating, molding, and curing.
The Importance of Vacuum Press Technology
Vacuum press technology plays a crucial role in various industries, offering numerous benefits, including:
- Even Pressure Distribution: Vacuum presses create a uniform pressure environment that is essential for consistent results.
- Reduced Air Bubbles: By removing air from the processing area, vacuum presses provide clear and smooth finishes.
- Shortened Processing Times: The efficiencies gained through vacuum pressing can lead to faster production cycles.
Benefits of Using Silicone Sheets for Vacuum Presses
When considering silicone sheets for vacuum presses, it's essential to understand their benefits, which include:
- Thermal Stability: Silicone sheets can tolerate high temperatures without degrading, making them perfect for high-heat applications.
- Flexibility and Versatility: They are adaptable for various shapes and sizes, accommodating unique product designs.
- Easy Maintenance: Silicone surfaces are easy to clean and maintain, which contributes to a longer lifespan.
- Low Friction: The smooth surface of silicone sheets reduces friction, allowing easy removal of materials without damaging them.
- Chemical Resistance: Silicone is resistant to many chemicals, ensuring durability in harsh working environments.
How to Choose the Right Silicone Sheet for Your Vacuum Press
Selecting the right silicone sheet is critical for optimizing your vacuum press performance. Consider the following factors:
1. Thickness of the Silicone Sheet
The thickness of the silicone sheet is paramount. Thicker sheets can provide better durability, while thinner options may be more flexible. Common thicknesses range from 0.5mm to 3mm.
2. Temperature Resistance
Ensure that the silicone sheet can withstand the specific temperature range relevant to your applications. Most silicone sheets can handle temperatures from -60°C to 200°C.
3. Size and Dimensions
Choose silicone sheets that match your vacuum press size. Custom-cut options are often available if standard sizes do not meet your requirements.
4. Application Needs
Identify the specific applications you will use the silicone sheet for, as specialized products are available for different uses, including laminating, shaping, and curing.
Applications of Silicone Sheets in Vacuum Presses
Silicone sheets are used in many applications, including:
- Laminating: Essential for adhering layers of materials together with precision.
- Molding: Invaluable in creating custom shapes and designs in various industries.
- Curing: Ideal for curing resins and adhesives without the risk of contamination.
- Protective Barriers: Used as barriers to protect the vacuum press from abrasive materials.
Maintenance Tips for Silicone Sheets
To preserve the longevity of your silicone sheets, adhere to these maintenance tips:
1. Regular Cleaning
After each use, clean the silicone sheets with warm, soapy water to remove any residue. Avoid harsh chemicals that may degrade the silicone material.
2. Proper Storage
Store silicone sheets in a cool, dry place away from direct sunlight to maintain their integrity over time.
3. Inspect for Wear and Tear
Regularly check for signs of damage or wear, such as cuts, tears, or discoloration, which may affect their function.
Comparative Analysis: Silicone vs. Rubber Membranes
While both silicone and rubber membranes serve similar purposes, they exhibit distinct characteristics:
Silicone Membranes
Silicone membranes are known for their higher temperature resistance and flexibility, making them suitable for applications requiring precision and durability.
Rubber Membranes
Rubber membranes, on the other hand, tend to be less expensive and may absorb liquids, which could lead to degradation in certain environments.
Conclusion
In conclusion, silicone sheets for vacuum presses are essential tools that can enhance the productivity and efficiency of your business operations. By understanding their features, benefits, and application processes, you can make informed decisions that optimize your production workflows.
For superior quality silicone sheets, consider purchasing from specialists like vacuum-presses.com. Our extensive selection includes various options tailored to meet your needs, ensuring you utilize the best materials in your vacuum pressing applications.
Embrace the versatility and efficiency of silicone sheets in your vacuum press today, and watch your business thrive with enhanced productivity and quality!
silicone sheet for vacuum press