In-Depth Exploration of Pressure Die Casting Tools in Metal Fabrication
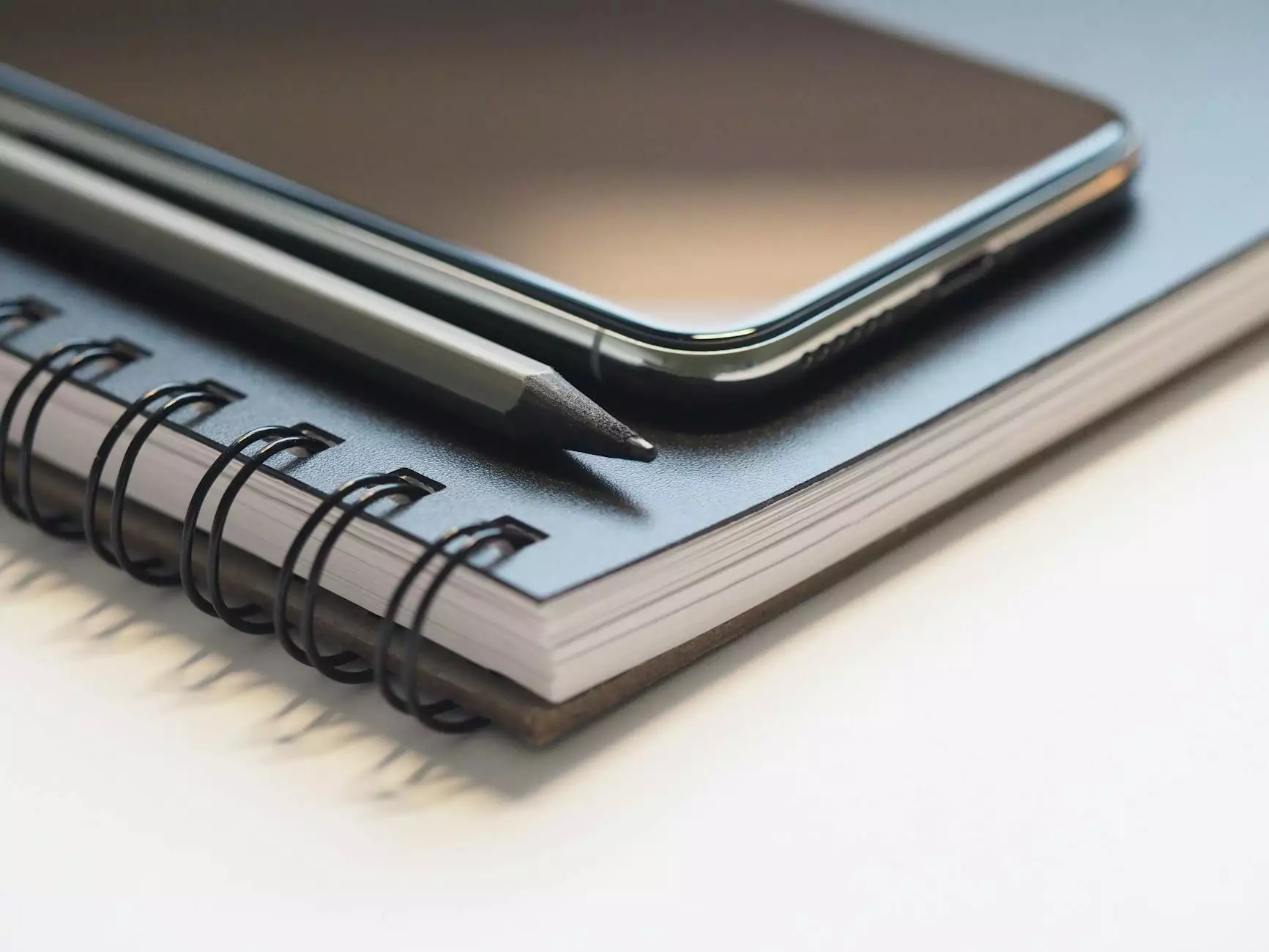
As the manufacturing industry advances, pressure die casting tools have become fundamental components in creating high-quality, precision metal parts. Whether you are a seasoned metal fabricator or just beginning your journey in metal manufacturing, understanding the nuances, applications, and innovations surrounding pressure die casting tools can significantly enhance your production capabilities. This comprehensive guide aims to shed light on every aspect of these tools, illustrating why they are indispensable in modern metal fabrication industries like deepmould.net.
Understanding Pressure Die Casting: The Foundation of Modern Metal Fabrication
At its core, pressure die casting is a manufacturing process where molten metal is injected into steel molds (dies) under high pressure. The process is celebrated for its ability to produce complex, accurate, and durable metal components at high volume, making it ideal across many sectors—including automotive, aerospace, electronics, and consumer goods.
What Are Pressure Die Casting Tools?
The pressure die casting tools consist of specialized machinery, precision-engineered dies, and auxiliary equipment designed to facilitate the casting process. These tools manage the flow of molten metal, maintain optimal pressure levels, and ensure that the final products meet stringent quality standards.
Components of Pressure Die Casting Tools
- Die Casting Machine: The central piece of equipment providing the hydraulic or mechanical force required for pouring metal into molds.
- Dies (Molds): Steel molds designed with intricate details, capable of withstanding high-pressure environments.
- Lubrication Systems: Reduce wear and facilitate smooth ejection of cast parts.
- Cooling Systems: Regulate temperature, maintain process stability, and prevent defects.
- Injection Units: Responsible for injecting molten metal under controlled pressure into the die cavities.
The Advantages of Utilizing Pressure Die Casting Tools in Metal Fabrication
Incorporating pressure die casting tools into manufacturing processes offers multiple benefits, making them a preferred choice for high-volume and precision-demanding productions.
1. Superior Dimensional Accuracy and Surface Finish
The high-pressure injection process results in parts with excellent dimensional tolerances and smooth surface finishes, often eliminating the need for secondary machining or finishing operations.
2. Complex Geometries and Intricate Details
This process allows for the creation of complex shapes with fine details, including undercuts, ribs, and textured surfaces that would be challenging with other manufacturing techniques.
3. High Production Efficiency
Once the dies are fabricated, multiple parts can be produced rapidly, making this method highly cost-effective for mass production scenarios.
4. Enhanced Mechanical Properties
The rapid cooling and solidification processes in pressure die casting contribute to strong, durable parts with minimal porosity, ensuring structural integrity.
5. Material Versatility
Commonly used materials include aluminum, zinc, magnesium, and other non-ferrous alloys, broadening the scope of applications according to project requirements.
Innovations and Technological Advancements in Pressure Die Casting Tools
The field of pressure die casting continually evolves, integrating cutting-edge technology to optimize performance and quality.
Smart and Automated Systems
Modern die casting machines now feature automation and computer control systems that monitor parameters such as pressure, temperature, and cycle times to ensure consistent quality and efficiency.
Modular Die Design
Developments in die design allow for modular molds, enabling faster setup times and easier maintenance, which are critical for large-scale production lines.
Energy-Efficient Technologies
New systems prioritize energy savings through improved insulation, efficient hydraulic systems, and waste heat recovery, aligning with sustainability goals.
Case Studies: Impact of Pressure Die Casting Tools on the Metal Fabrication Industry
Automotive Industry
Leading automakers utilize pressure die casting tools to produce engine blocks, transmission cases, and structural components. The high precision and repeatability of these tools reduce weight without compromising strength, thereby improving fuel efficiency.
Aerospace Sector
In aerospace, components require stringent tolerances and superb quality. Pressure die casting tools enable the manufacturing of complex aerospace-grade parts with minimal defects, ensuring safety and performance.
Consumer Electronics
Small, intricate electronic housings benefit from advanced die casting tools that can produce high-detail parts in large volumes, accelerating product time-to-market.
Choosing the Right Pressure Die Casting Tools for Your Business
Selecting appropriate tools is critical for achieving desired production outcomes. Consider the following factors:
- Material Compatibility: Ensure the tools can handle the specific alloys used in your projects.
- Production Volume: High-volume manufacturing benefits from durable, high-speed machines with rapid cycle times.
- Part Complexity: Advanced die design can accommodate intricate geometries and fine details.
- Budget and Investment: Balance initial costs with long-term savings from efficiency and reduced scrap rates.
- Technological Features: Opt for machines with automation, sensors, and smart controls for optimal performance.
DeepMould.net: Leading Provider of Premium Pressure Die Casting Tools
At deepmould.net, we specialize in delivering state-of-the-art pressure die casting tools tailored to meet the specific needs of our clients in the metal fabrication industry. Our comprehensive range of products includes:
- High-precision die casting machines
- Custom-designed dies and molds
- Advanced injection systems
- Maintenance and upgrade solutions
Partnering with us means gaining access to innovative technology, expert support, and a commitment to excellence—all essential for elevating your manufacturing processes and achieving superior product quality.
Future Trends in Pressure Die Casting Tools and Metal Fabrication
The trajectory of pressure die casting tools points toward increased automation, IoT integration, and sustainability initiatives. Expected advancements include:
- Artificial Intelligence (AI): For predictive maintenance and process optimization.
- Robotics: Enhanced automation for high-precision, low-error operations.
- Sustainable Materials: Development of eco-friendly alloys and recyclable dies.
- Digital Twin Technology: Virtual simulation of casting processes to foresee issues and improve designs before physical production.
Conclusion: Why Investing in Top-Quality Pressure Die Casting Tools Is Vital for Your Business Success
Investing in high-quality pressure die casting tools is more than a technological upgrade; it's a strategic move towards optimizing productivity, improving product quality, and reducing costs. As industries move towards more complex and demanding manufacturing requirements, the importance of reliable, innovative die casting equipment cannot be overstated.
Whether you're looking to expand your capacity or enhance existing processes, partnering with a trusted provider like deepmould.net guarantees access to cutting-edge solutions designed to support your growth and ensure your products stand out in a competitive market.
Embrace the future of metal fabrication with pressure die casting tools that deliver precision, speed, and excellence—your gateway to manufacturing superiority.